Doctoral Candidate | Mining Engineering
University of Alberta (Canada)
Advisor: Derek Apel
Itasca Mentor: Tatyana Katsaga

Introduction
In underground stopes, energy alternation and stress transmission happens along the interfaces of backfilled stopes and the surrounding rock mass due to ubiquitous mechanical interactions between them. In this study, the stress state variation law in cemented rockfill and underground backfilled stopes, the strength characteristics of rockfill material, and the stability of backfilled stopes will be simulated using coupled PFC3D/FLAC3D software to develop linked discrete/continuum models that incorporate in-situ and laboratory experiments.
Five aspects of research contents, mainly about the strength characteristics of cemented rockfill and mechanical interactions between cemented rockfill and surrounding rocks in underground backfilled stopes, will be involved in this study. The research materials and data will be collected from a mine, and the laboratory experiments will be carried out in the Rock Mechanics Lab at the University of Alberta.
Numerical Modeling of Cemented Rockfill Material under Uniaxial and Triaxial Compression Based on Discrete Element Method
In this part, a material-modeling support package imbedded in the software PFC3D was adopted, and numerical uniaxial and triaxial compression tests were carried out on both bonded-particle models (BPMs) with the simplified particle size distribution and the mean weighted particle diameter of the cemented rockfill (CRF) material, of which the microstructural parameters were both well calibrated to ensure the macro-mechanical properties of these BPMs perfectly corresponded to the laboratory testing data of the real CRF core specimens. The strength characteristics and failure pattern of the CRF BPMs under numerical triaxial compression were calibrated and the modeling results highly agreed with the laboratory testing results according to the Mohr-Coulomb strength criterion. The particle size distribution and the model-particle diameter ratio of these BPMs also significantly influenced the macro-mechanical properties and fracture evolution of the BPMs.
Numerical Modeling of Direct Shear Test on Cemented Rockfill Material Based on the Coupled Finite Difference and Discrete Element Method
This part provides an effective determination process of the interface of microstructural parameters in the numerical modeling of the mechanical interaction between the backfill column and the surrounding rocks by using the coupled finite-difference and discrete-element (FD-DE) method. Three-dimensional numerical direct shear tests were conducted on the coupled FD-DE model of the combined rock-cemented rockfill (R-CRF) specimens with the frictional-bonded interface. With the microstructural parameters determined, the macro-mechanical properties of the interface of the coupled model were calibrated to fit well with the theoretical values of the combined specimen under the direct shear condition assumed according to the Mohr-Coulomb strength criterion. Evident elastoplastic shear behavior was observed on the interfaces, and excellent agreement was attained between the shapes of the theoretical and simulated shear stress-displacement curves of the coupled models at different servo-controlled normal stresses. The test results validated the feasibility and rationality of the coupled FD-DE method for modeling the combined specimens with frictional-bonded interfaces or joints.
Numerical Modeling of Shear Behavior at Interface between Backfill Column and Surrounding Rock Based on Coupled Finite Difference and Discrete Element Methods
In this part, a 1000-meter-deep underground stope was excavated in the numerical model created with FLAC3D by the finite difference method (FDM) and then backfilled with cemented rockfill (CRF), which was created with PFC3D by the discrete element method (DEM). The shear behavior at the interface of the CRF column and surrounding rock was simulated by the wall-zone coupling method (WZCM) through Socket 0/1 connections. The modeling results illustrated that during the settlement and consolidation of the CRF particles, a weak binding effect formed at the interface and an arching phenomenon occurred inside the CRF column, which significantly influenced the stress and displacement distributions inside the columns. Meanwhile, backfilling with CRF efficiently improved the stress variation at the pillar and reduced the rockburst risk at the stress concentration zones.
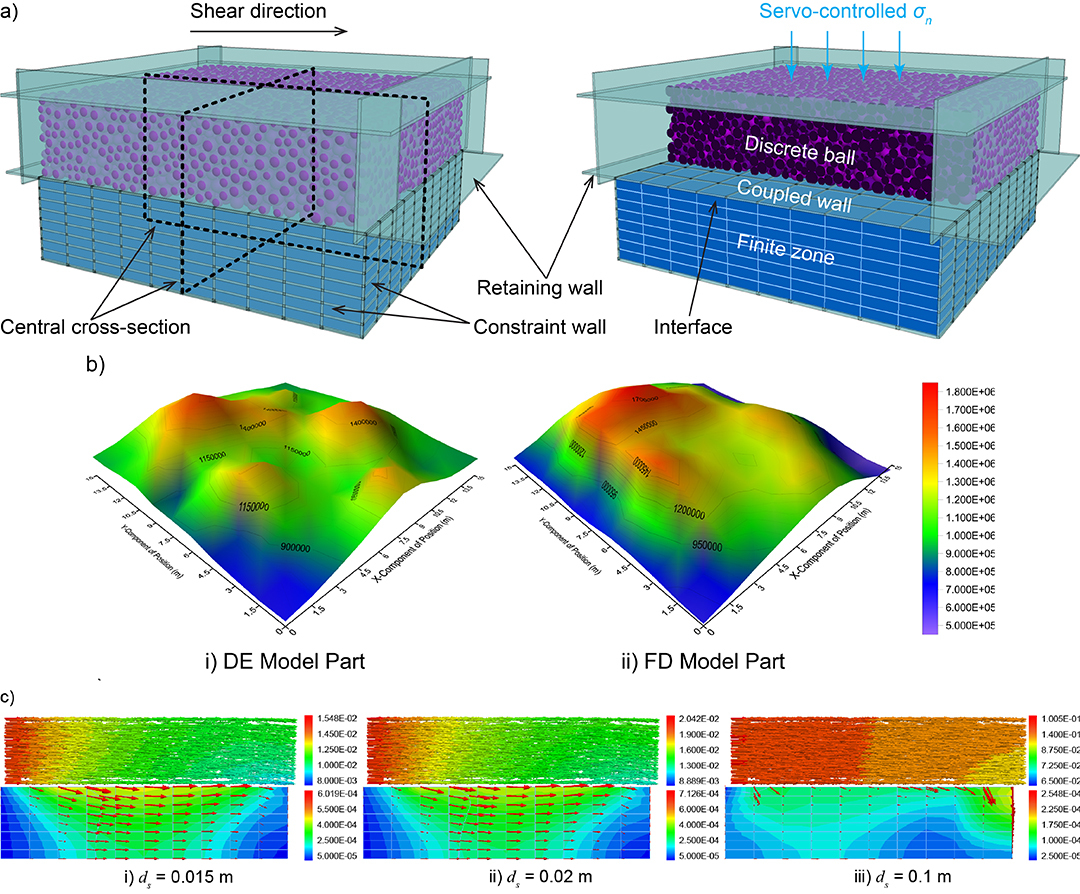
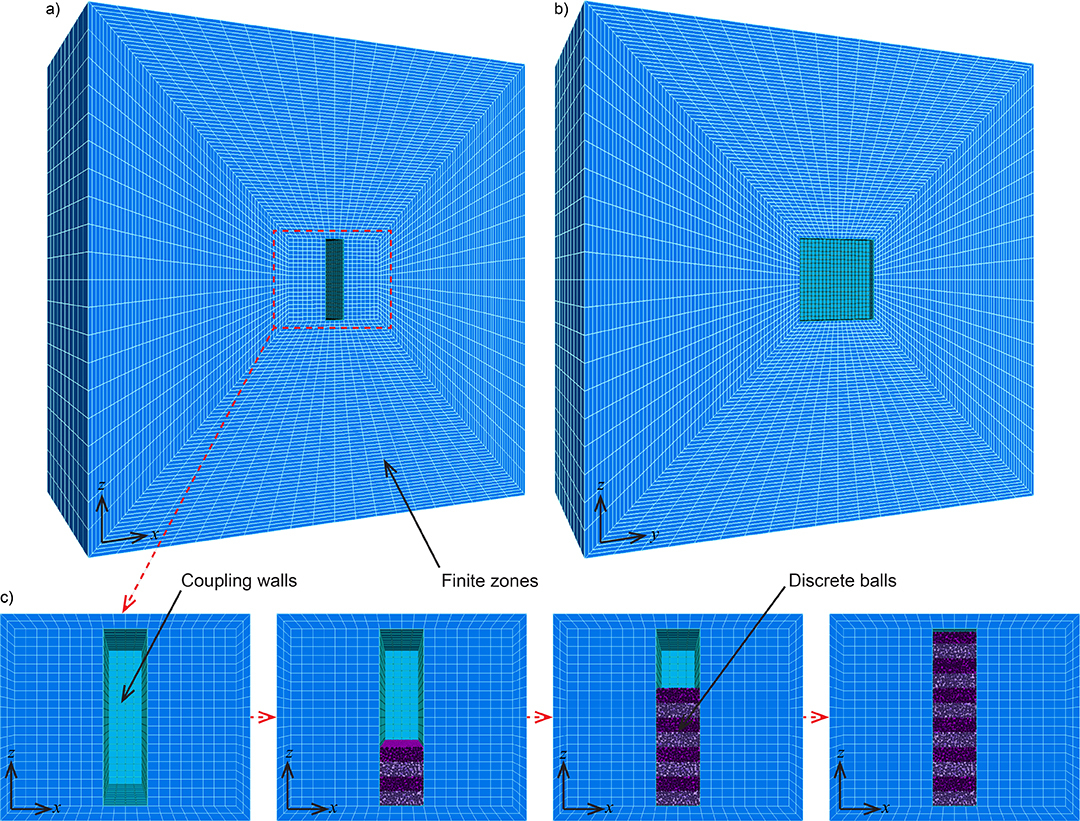
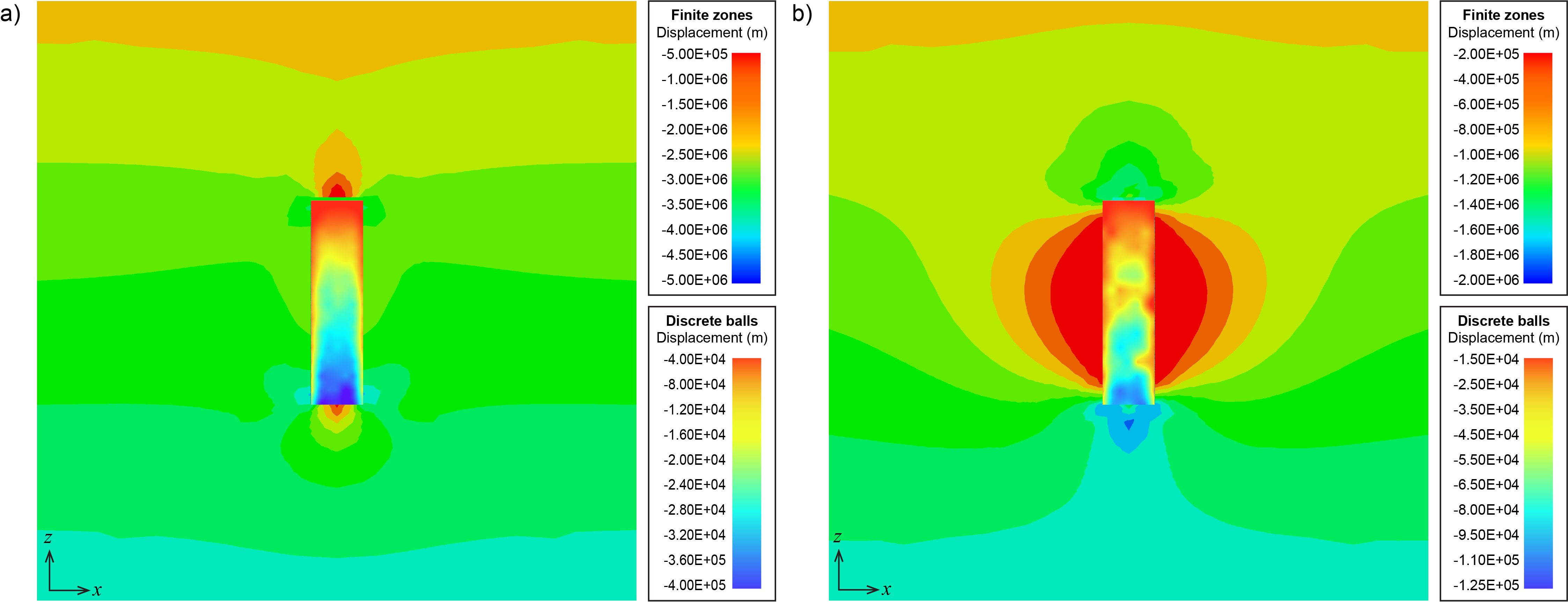
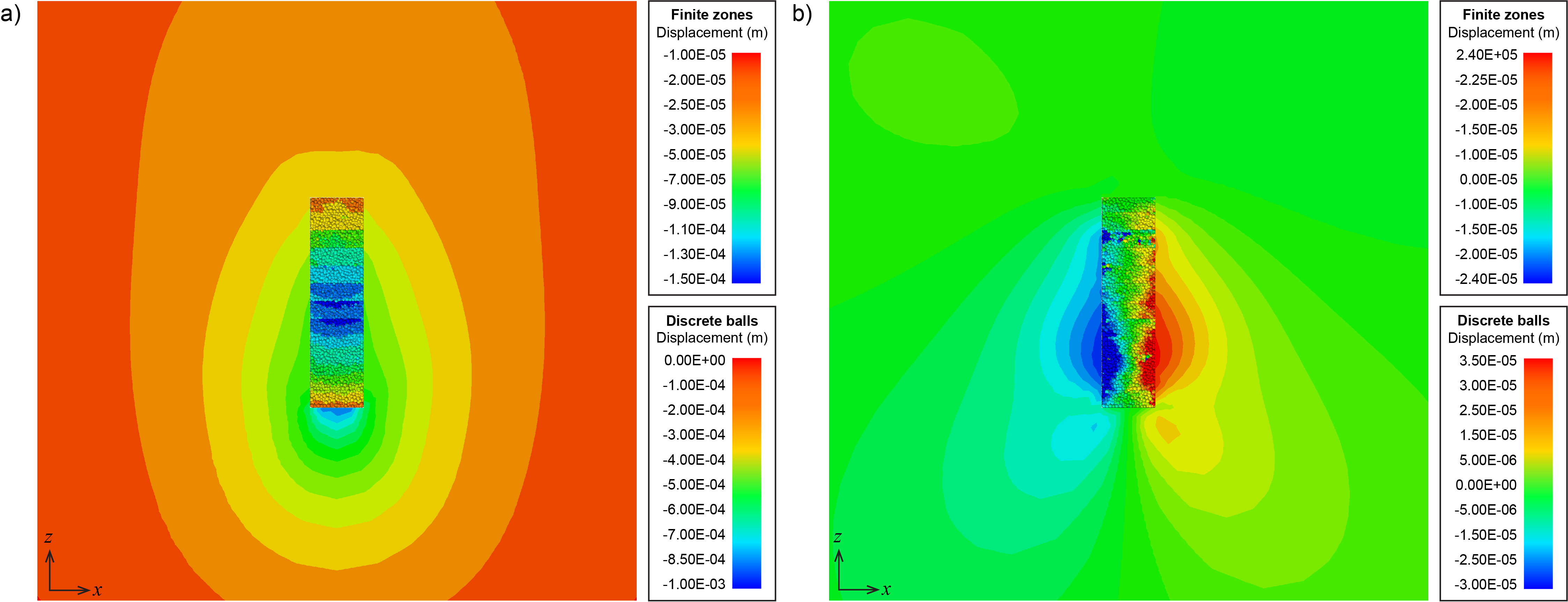