Simulating Spalling With a Flat-Jointed Material
PROJECT DESCRIPTION
Long-term storage of spent fuel is critical to the nuclear energy industry. The Swedish Nuclear Fuel and Waste Management Company (SKB) is developing an approach for the storage of spent nuclear fuel in an underground repository in competent crystalline rock. One design challenge is that the induced stresses at the borehole walls may be greater than the rock mass strength, which would result in an excavation damaged zone (EDZ) around the boreholes. In competent crystalline rock, the EDZ takes the form of spalling on the excavation boundaries. This damage process needs to be better understood in order to evaluate its impact on repository performance.
In order to better understand the damage process, an in-situ test involving the drilling of two boreholes was performed in Äspö diorite at SKB’s underground hard rock laboratory in Äspö. Tests and monitoring were performed on the pillar that separated the boreholes.
In order to further investigate the damage process, numerical modeling was used.
ITASCA'S ROLE
The numerical modeling of the boreholes and their pillar was performed by Itasca using PFC2D and PFC3D models as well as a set of coupled FLAC3D-PFC3D models. PFC’s ability to use a flat-jointed material contact model to simulate spalling was evaluated, where both 2D and 3D flat-jointed materials were created to simulate the crystalline Äspö diorite.
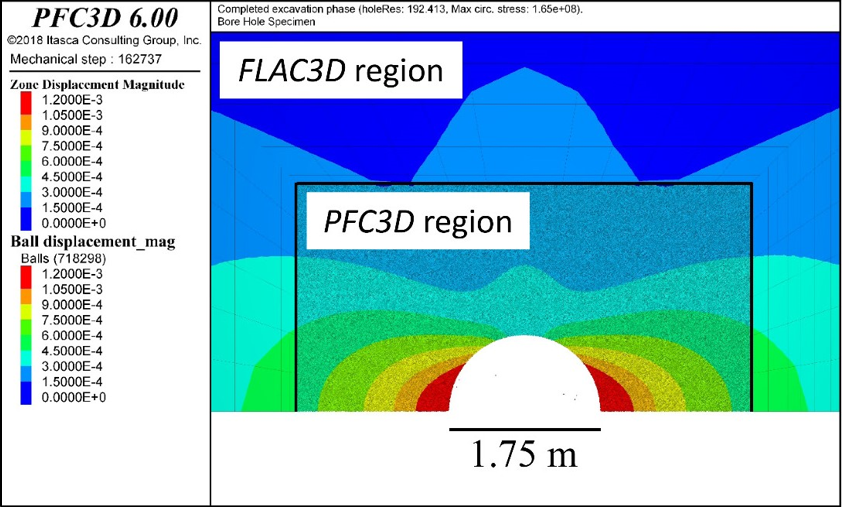
PROJECT RESULTS
From evaluating the PFC flat-jointed material model used to simulate spalling, the following was observed:
- Spalling can be modeled using the PFC3D flat-jointed material.
- The coupled FLAC3D-PFC3D borehole models presented a compatible displacement field across the coupling interface (Figure 1). The coupled model also ran much faster, enabling the simulation to run in a reasonable amount of time.
- The model simulated damage consisted of a spalling zone and two damage lobes, as seen in Figure 2. The spalling zone corresponds with an early stage of rock mass yielding before a notch has formed.
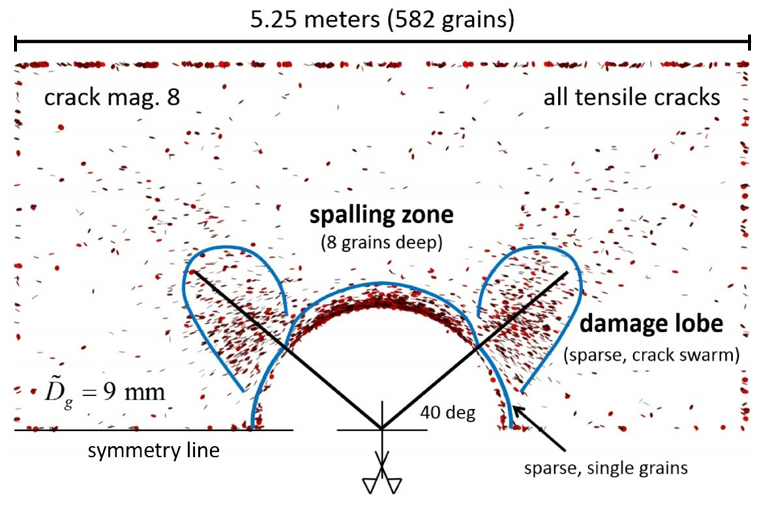
REFERENCES
Potyondy, D., and Mas Ivars, D. (2020) “Simulating spalling with a flat-jointed material,” Applied Numerical Modeling in Geomechanics 2020 (Proceedings, 5th International Itasca Symposium, February 2020), paper 03-01. Minneapolis, Minnesota: Itasca