The thermal module of PFC allows simulation of transient heat conduction and storage in materials consisting of PFC particles, as well as development of thermally induced strains and forces. PFC supports both thermal-only and coupled thermal-mechanical analysis. The thermal material is represented as a network of heat reservoirs (associated with each mechanical body) and thermal contacts (associated with each mechanical contact). Heat flow occurs via conduction in the active thermal contacts that connect the reservoirs. Radiative and convective heat transfer are not included in the present formulation. Thermally induced strains are produced in the PFC material by modifying the particle size. Mechanical contact models may also account for thermally induced forces.
A thermal contact is associated with each mechanical contact, but only some of these contacts are active. By default, a thermal contact is active if the corresponding mechanical contact is active. However, thermal contacts can be inhibited with custom criteria if more flexibility is desired. Once the thermal micro-properties are specified, subsequent loading or damage (i.e., bond breakages) will modify the number of active pipes and thereby change the ability of the material to conduct heat. For example, as a bonded material is compressed and new active contacts form, the macroscopic thermal conductivity will be increased, but as bonds break and contacts become inactive, the macroscopic thermal conductivity will be reduced.
The thermal model in PFC simulates the transient flux of heat in materials (conduction and storage in materials) and the subsequent development of thermally induced strains and forces.The thermal model may be run independently or coupled to the default mechanical model. Thermal strains are produced to account for heating of both particles and bonding material. Walls also may be assigned a temperature to act as a thermal boundary condition.
The thermal material is represented as a network of heat reservoirs (associated with each mechanical body) and thermal contacts (associated with each mechanical contact). Heat flow occurs via conduction in the active thermal contacts that connect the reservoirs. Radiative and convective heat transfer are not included in the present formulation. Thermally induced strains are produced in the PFC material by modifying the particle size. Mechanical contact models may also account for thermally induced forces. Once the thermal micro-properties are specified, subsequent loading or damage (in the form of bond breakages) will modify the number of active pipes, and thereby change the ability of the material to conduct heat. For example, as a bonded material is compressed and new active contacts form, the macroscopic thermal conductivity will be increased; but as bonds break and contacts become inactive, the macroscopic thermal conductivity will be reduced.
As an example, a planar sheet of some width is initially at a uniform temperature of 0°C. The left side of the sheet is then exposed to a constant temperature of 100°C, while the right side is kept at 0°C. The sheet eventually reaches an equilibrium state at a constant heat flux and unchanging temperature distribution. Contour of ball temperature and thermal power vector field for a hexagonal packed system is shown below on the left. Modeled and analytical (Crank, 1975) normalized temperature distributions within the sheet, as a function of distance from the left side and time, are shown below on the right.
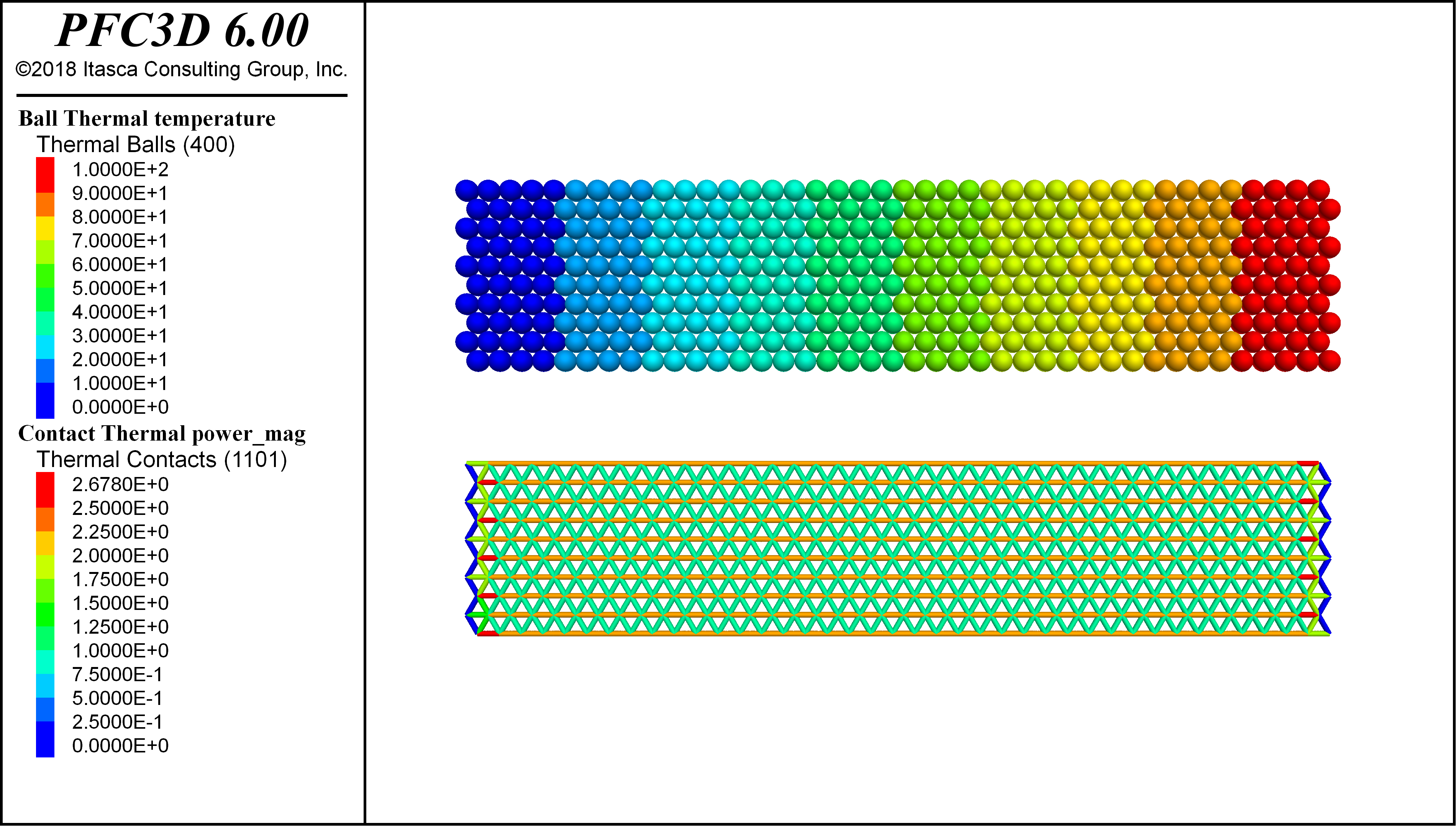
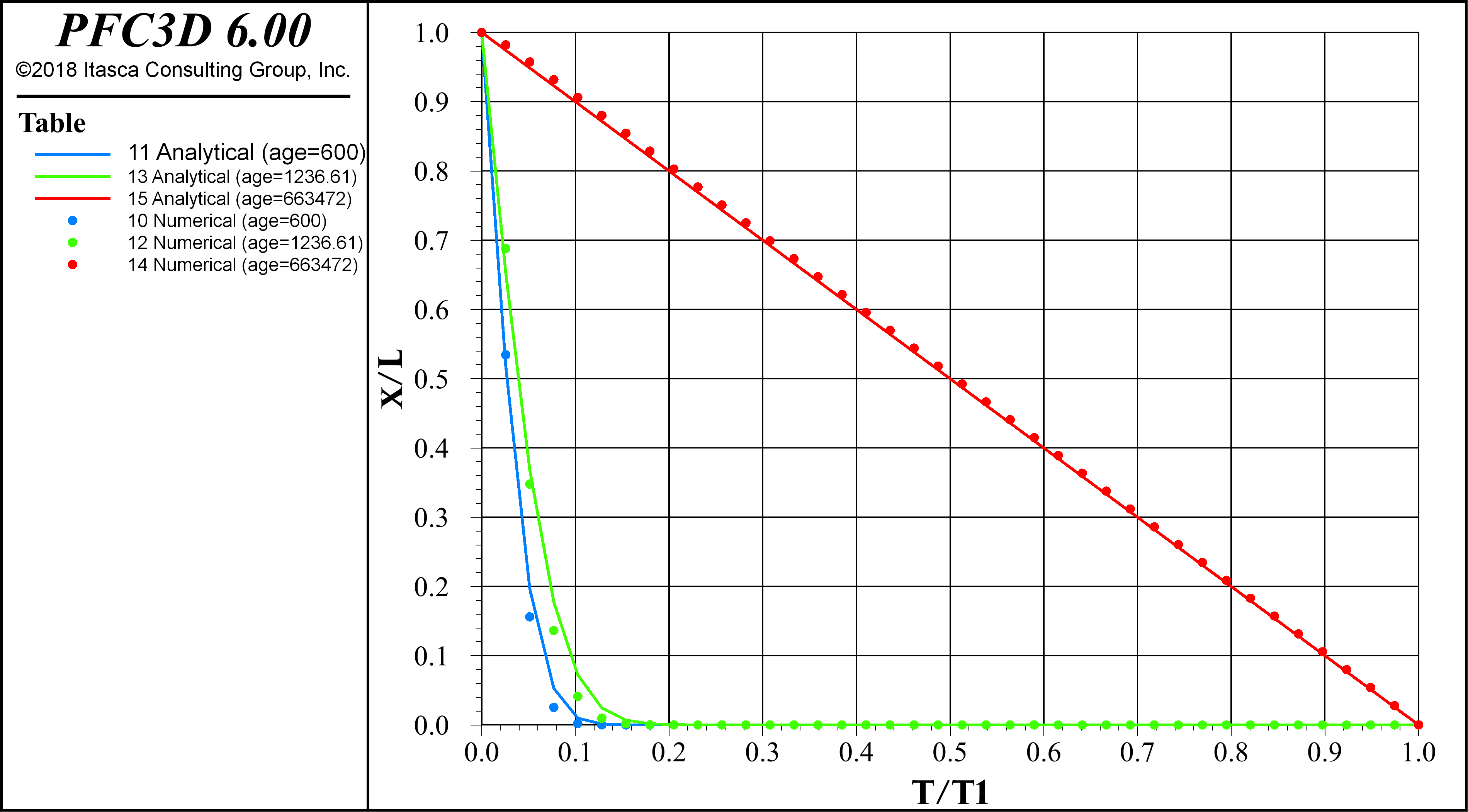